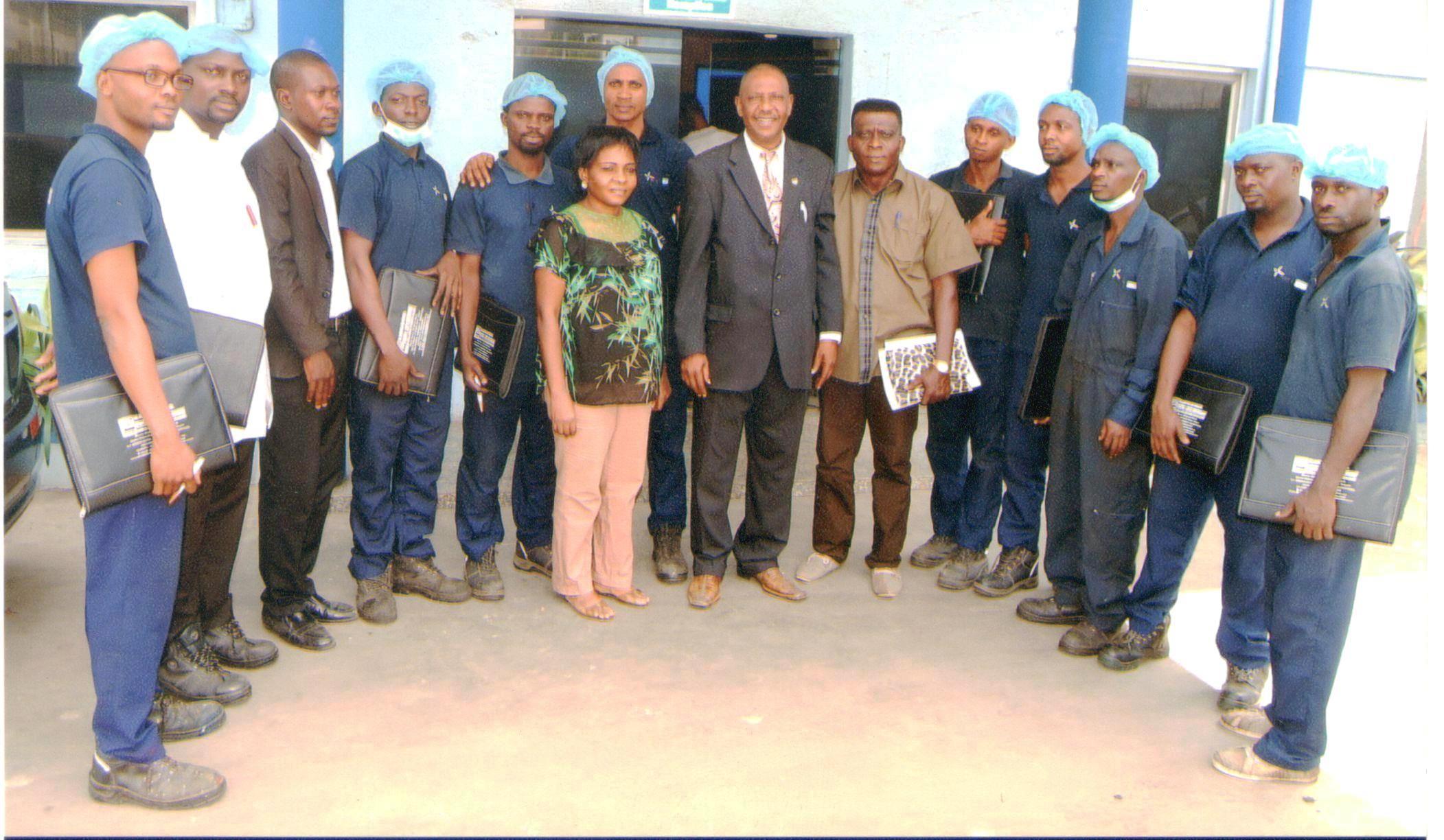
Managing Health, Safety and Environment In Organizations
By
DR OLANIYI OPANUGA FNIPM, FIoMD, FISOM, FOHSE, COPOM©
Chief Consultant/CEO
OPTIMUM RESOURCES LTD
1.0 INTRODUCTION
The Federal Government and responsible Corporate Nigeria place high premium on good Health, Safety, and Environmental (HSE) Management Practices. In order to protect employees, property and the environment certain laws both common law and legislation which prescribe specific rules concerning occupational health, workplace safety and environmental protection have been put in place. There are concerned international bodies such as the United Nations Environmental Programme (UNEP) World Health Organization (WHO), International Labour Organization and local agencies such as the Federal Environmental Protection Agency (FEPA) and its State counterparts e.g Lagos State Environmental Protection Agency (LASEPA). The Federal Ministries responsible for Labour and Productivity, Science & Technology, Transportation, Health, Industry Trade and Investments, Environment etc also monitor industrial activities. Factory and facility inspection is carried out by various governmental agencies guided by legal provisions such as the Factories Act 1990, later updated with the factories Act Cap F1 Laws of the Federation of Nigeria, Labour Act 2004, Environmental Impact Assessment Act, the Land Use Act, Harmful Waste, Nuclear Safety and Radiation Protection Act, Cap. W6, LFN 2004 Oil Pipelines Act, Animal Diseases Control Act, Workmen’s Compensation Act, Cap.W6 LFN, 2004 and other legislation and regulations. However, there are reported cases whereby certain organizations have been indicted by the law courts for bad HSE practices affecting either the employees, consumers or the community. The law setting up certain relevant agencies such as the National Agency for Food, Drug Administration and Control (NAFDAC) and the Standards Organization of Nigeria (SON) empower them to play effective complimentary roles. Consumer protection and quality assurance management activities are inextricably tied to HSE in several ways. For instance an unhealthy workforce, unsafe workplace or an unprotected environment cannot produce safe and quality products for the people.
2.0 BEYOND THE LAWS
Preventing incidents or accidents and working at eliminating near-miss events, causes of diseases and accidents will help us to prevent illnesses and fatalities. The factories Act Cap F1 LFN 2004 formerly factories Act 1990 and Decree No 16 of 1987 is the statue regulating the protection of safety health and welfare of workers with a view to ensuring that workers are not exposed to hazardous at work. There are provisions aimed at preventing accident, and industrial diseases, the process of accident, notification, investigation, reporting and records, the duties of factory inspectors, dealing with offences, penalties and legal proceedings against companies that breach these provision; An incident is a foreseeable and preventable event that may result in undesirable situation but not serious enough to cause pain or loss (such as near-miss situation) while an accident is foreseeable and preventable event or circumstance that results in personal injury, damage to property or loss of life. Designing the right HSE or SHE process and taking preventive measures can ward-off incidents and accidents in the work place.
Incidents and accidents are predictable and preventable even though they are both “unplanned” events.
The laws clearly state specific and general duties and obligations of employers and employees. In other areas not clearly spelt out by the laws common sense, customs and morality are expected to fill the lacuna. Therefore, health, safety and environmental issues border on both legality and moral values, or if you like corporate social responsibility. Every responsible corporate citizen should look beyond what the law stipulates on any HSE related issue. The focus of every organization should be on achieving:
- Sound Occupational Health
- Zero Accident
- Environmental Protection
But the extent to which these are done will depend on the influences of the parties involved. See fig. 1.
3.0 HEALTH
Health is a state of physical, mental and social well being of an individual. The World Health Organization (WHO) insists that health is not just the absence of disease or infirmity. When someone is sound physically, psychologically and emotionally, we refer to that person as being healthy. Factories Act 2004 part II-Health (General Provisions) stipulates that every factory shall be kept in a clean state, free from dirt arising from any drain, sanitary convenience or nuisance, and without prejudice to the generality of the provisions. The plant should be designed and provisions made in such a way to ensure:-
- Cleanliness
- Avoiding of Overcrowding
- Proper Ventilation
- Adequate Lighting
- Drainage of Floors
- Adequate provision of Sanitary Conveniences
- Provisions of Protective Clothing and appliances
- Provisions of meals in certain dangerous trades.
Associated with the above is the welfare issue concerning provision (by employers) of:
- Adequate clean/drinking water
- Washing facilities.
- Accommodation for clothing (i.e cloakroom).
- A clinic in the factory or nearby
- First Aid for the treatment of small ailments and minor injuries at work
Worker’s rights include one hour break per day (8 hours work) one day rest in every seven days, working for not more than 40 hours per week (under the National Minimum Wage Act, 2011) but not in the Labour Act. General working hours are fixed by mutual agreement or collective bargaining within the industry or organization. And there is right to enjoy annual leave with pay.
All these are the provisions of the law (Labour Act and Factories Act). The intention of government is to guarantee good health and healthy working environment for the workers. The following are worthy of note during SHE/EH&S Training at Optimum Resources Safety Institute (ORSI);
3.1 Identification & Recognition of Risks And Hazards (Job Hazard Analysis-JHA)
3.2 Diseases Associated With Workers in Industries
3.3 Habits Associated With Industrial Hazards and Occupational Health Problems
3.4 Epidemiology In Occupational Health
3.5 Death Prone Exposures
- Mechanical
- Electrical
- Chemical
- Fire
- Civil Work-related e.g Underground, at Height and Construction Projects.
- Gases e.g Hydrogen Sulfide (H2S)
- Radioactive Hazardous Materials
- Snake Bites and wild animal attacks
- Slip, Trip and Fall etc
3.6 Control of Exposures Against Morbidity And Mortality
4.0 SAFETY
Safety can be defined as freedom from danger, harm or threat. Another word
for safety could be ‘protection’. One may be safe even in the face of risk and
hazard provided the risks are low and the hazards are controlled. The watch word are ‘low’ and “control”, since human beings cannot avoid risks and hazards in industrial (and, in domestic and social) environment, it is only sensible to find a way around them. That is why we must emphasize the duty of reasonable of care as well the need for risk assessment and hazard control. Every little human activity involves an element of risk (e.g walking, running or driving) and many useful things can also be hazardous (e.g water, industrial chemicals, food, pharmaceuticals etc).
As a lecturer at the College of Production & Operations Management (COPOM), I always advise Health and Safety engineers and managers to step up their career with further education and training. For instance, studying to earn a Post-Graduate Diploma (PGD) or Master’s in HSE Management won’t be a bad idea. Registering with HSE/SHE professional bodies is mandatory for a true safety practitioner.
At the Centre For Occupational Health, Safety And Environment, College of Production And Operations Management (COPOM) we preach Zero Accident and teach to proof that accidents or incidents are preventable or avoidable. Beyond this, we teach how organizations can manage their SHE or EHS for results. We expect employers and management to put in place the right HSE policies, procedures, facilities, education and training programmes, rules and regulations, incentives and controls in line with the relevant laws and ethics.
We also expect the workers to take advantage of these by obeying safety rules, adopting safer ways of performing their duties and conducting themselves in a safe manner always.
In line with the Factories Act 2004 employers are mandated to protect employees from hazards which the following may pose:-
- Prime Movers
- Transmission Machinery
- Vessels Containing dangerous liquids
- Hoist and Lifts
- Dangerous Fumes
- Fire
- Means of Access
The law emphasizes the security fencing of all dangerous parts of machinery whether in use or not. It also stresses the provision of safety equipment and tools.
5.0 ENVIRONMENT
An environment (here we are concerned with immediate environment) is the geographical area in which people live and work and in which an organization operates. The environment in which an organization carry out its activities is important for the following reasons:-
- It provides resources e.g land, labour, raw materials, climate etc.
- It provides markets i.e consumers.
- It provides protection i.e government protective policies, security and general laws.
- It sustains the operations generally.
5.1 Environmental Impacts And Industrial Activities
The issues of environmental concern include:-
- Environmental Pollution
- Global Warming
- Ozone Layer Depletion
- Air Pollution
- Water Pollution
- Ground Water Pollution
- Habitat Destruction.
- Chemical Hazards
- Hazardous Wastes
- Waste/Waste Water Disposal
- Environmental Diseases.
5.2 Global and National Concern
The activities of the United Nations Environmental Programme (UNEP), the
Occupational Safety and Health Administration (OSHA) and the Federal
Environmental Protection Agency (FEPA) and others will be fully discussed
in the Advanced HSE programme. But suffice it to say that concern is growing
to adopt the following:
- Clean Air
- Clean Water
- Clean Production
- Green Manufacturing(and Green Business)
- Environmental Impact Assessment (EIA) Systems
- Resource Conservation e.g. afforestation, waste re-cycling, strict regulations on tree falling and mandatory tree planting, protection of forest reserves etc.
- Sustainable Production e.g Biofuels and allied renewable energy sourses
6.0 THE IMPORTANCE OF HSE MANAGEMENT
(a) To the individual, good HSE practices are beneficial
(b) To organizations, good HSE management can yield great dividend.
(c) To the nation, the benefits are legion.
7.0 SMART WAYS TO PREVENT ACCIDENT AT OPERATIONAL LEVEL
Optimum Resources Safety Institute (ORSI) listed 50 ways. Here are some of them:
- Work in a safe work place.
- Adopt safe work practices e.g use your Personal Protective Equipment (PPE) effectively.
- Ensure everything is in its proper place. Think 5S.
- Take Good Housekeeping and Hygiene seriously.
- Together, let us promote a safe workplace, safe work practices and right safety behaviours.
- Take Professional Certificate or Diploma course on Safety for your personal protection, career and professional development.
- Only a safe worker can be productive and only productive people become successful. Join professional bodies such as the Society of Safety, Health And Environmental Management (SOHSEM), the Institute of Safety Health And Environmental Management (ISHEM), and the Institution of Security Operations Management (ISOM), the Nigerian Institute of Production Management (NIPM) and the Institute of Operations Management Development (IoMD) to boost your career!
Contact us at COPOM or Optimum Resources Safety Institute (ORSI) for guidance or advise to help you take rewarding decision of a life time.
Occupational Health, Safety and Environmental Practices |
International Laws And Conventions |
Civil Societies |
The Community Traditions |
Corporate Management HSE Policy & Culture |
Government Policies, Laws and Regulations |
Ownership Values of Employees |
General Public Awareness |
Workers/ Labour Unions |
Fig.1: Factors Affecting HSE Practices In Industry- Dr. Olaniyi Opanuga
8.0 CONCLUSION
Organizations need to comply with the legal provisions on Environment, Safety and Health. Management needs to put control measures in place and provide regular safety training for employees.
Rudimentary knowledge of HSE management is quintessential for all workers. This can be built upon from time to time as there are different levels of safety education and training. The issues of health, safety and environment should be taken seriously by all the stakeholders especially management and the employees. Everyone is expected to play his or her own role, so that we will savor good health, be safe and make our environment a better habitat for happy living. Health is wealth. Our behaviours should not be animalistic or reckless. Our lives are in our own hands. We should be our brother’s keeper. We should keep learning better and safer methods of doing things to enhance the protection of ourselves and our fellow humans. As organizations we can design better health and safety process, mount effective programmes and improve our safety culture.
0 Comment